Сварка – один из основных способов соединения металлических конструкций. Ее используют как в домашнем хозяйстве, стройке и ремонте, так и в производственной, военной и даже космической отраслях. Чем более ответственное соединение – тем выше требования к его прочности, качеству и надежности.
По разным причинам в сварных соединениях могут встречаться дефекты, которые снижают их прочность, герметичность и долговечность, что критически важно для безопасности эксплуатации изделий и конструкций.
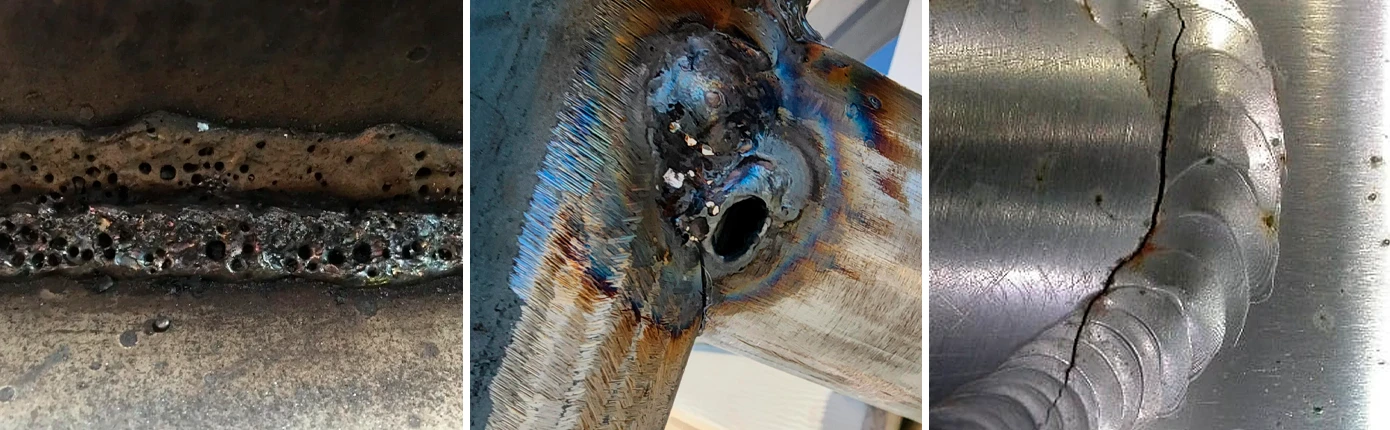
Дефекты сварных швов представляют собой отклонения от требований стандартов и технических условий, возникающие при выполнении сварочных работ. Основные причины дефектов сварных соединений – некачественные материалы и инструменты, неверная техника и режимы сварки.
Качество сварки и сварных швов регламентируются специальными требованиями и стандартами, например, ГОСТ 30242-97 «Дефекты соединений при сварке металлов плавлением. Классификация, обозначение и определения». Этот документ определяет виды дефектов, их допустимость и методы контроля.
Среди наиболее значимых документов, регламентирующих требования к качеству сварки и контролю дефектов, можно выделить:
- ГОСТ 30242-97 – Дефекты соединений при сварке металлов плавлением.
- ГОСТ 5264-80 – Ручная дуговая сварка. Соединения сварные.
- ГОСТ 16037-80 – Соединения сварные стальных трубопроводов.
- ГОСТ 14771-76 – Дуговая сварка в защитном газе. Соединения сварные.
- ГОСТ 23118-2012 – Конструкции стальные строительные. Общие технические условия.
- ГОСТ 3242-79 – Соединения сварные. Методы контроля качества.
- ГОСТ 14772-86 – Контроль неразрушающий. Соединения сварные. Методы ультразвуковые.
Виды дефектов сварных швов
Дефекты делятся на внешние (наблюдаемые визуально) и внутренние (выявляемые с использованием специальных методов контроля). Они классифицируются по характеру, степени влияния на эксплуатационные свойства и требованиям к исправлению.
Наружные дефекты сварных швов
Эти дефекты проявляются на поверхности шва и обнаруживаются при тщательном визуальном осмотре или измерительными приборами:
- подрезы – углубления вдоль края шва;
- наплывы – излишки металла шва на поверхности основного металла;
- кратеры – углубления на поверхности шва;
- прожоги – сквозные отверстия в металле.
Внутренние дефекты сварных швов
Находятся внутри шва или области нагрева, их обнаружение требует использования специализированных методов неразрушающего контроля:
- поры – пустоты внутри шва;
- трещины – разрывы металла;
- свищи – сквозные отверстия, соединяющие внутреннюю и внешнюю поверхность шва;
- посторонние включения – наличие в структуре шва примесей шлака, грязи и т.д.
Сквозные дефекты сварных швов
Сквозные дефекты, например прожоги или трещины, критически опасны, т.к. полностью нарушают герметичность соединения. Видны с обеих сторон детали или конструкции.
Классификация дефектов сварных соединений
ГОСТ 30242-97 делит дефекты на допустимые и недопустимые. Перечислим основные виды дефектов.
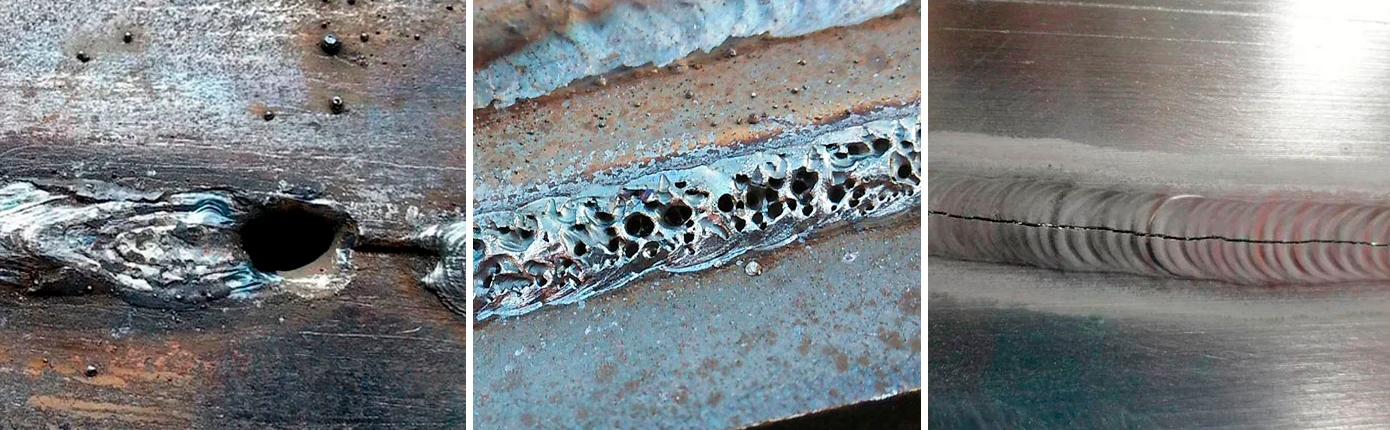
Прожоги – чрезмерное проплавление металла с образованием отверстия. С обратной стороны прожога может образоваться наплыв. Дефект возникает из-за избыточной температуры, слишком медленного ведения электрода, большого расстояния между краями деталей. Чаще встречается на тонких листах металла. По ГОСТу допускается только в некритичных соединениях.
Поры – мелкие газовые полости внутри шва. Причиной возникновения пор в сварном шве может быть загрязнение поверхности, недостаточная защита сварочной зоны от контакта с воздухом, большой процент углерода в присадочном материале, влажные электроды. Газовые поры в сварном шве допустимы в ограниченном количестве, зависящем от класса прочности изделия (ГОСТ 5264-80, ГОСТ 14771-76), недопустимы в герметичных и ответственных соединениях (ГОСТ 30242-97).
Трещины– разрушения внутри шва или зоны термического влияния. Образуются из-за внутренних напряжений, неправильного режима охлаждения, неверной стыковки деталей или неудовлетворительной подготовки металла. Трещины могут быть горячими – возникать в процессе сварки и холодными – появляются после остывания металла. Независимо от типа, трещины недопустимы во всех соединениях.
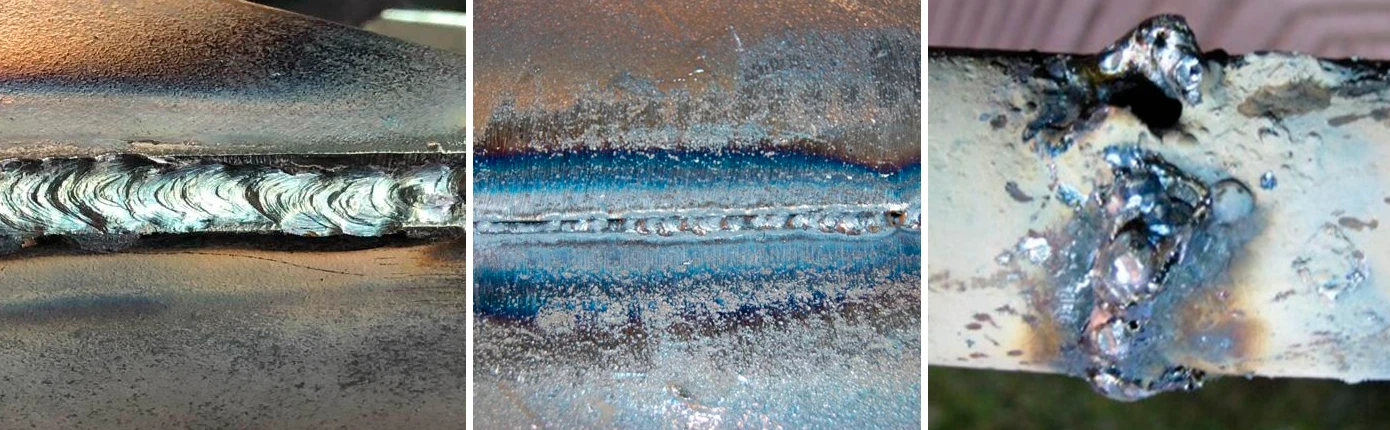
Подрезы – углубления вдоль границы шва. Такая «бороздка» вдоль шва уменьшает его сечение, что сказывается на прочности. Причина – неправильный угол наклона электрода или повышенный сварочный ток. Частично допустимы в соответствии с ГОСТ 16037-80, ГОСТ 23118-2012 (глубина до 0,5 мм).
Непровары – отсутствие сплавления между металлом основы и швом. Непровар в сварном шве может появиться из-за недостаточного прогрева металла, загрязнений, неправильного угла или слишком быстрого ведения электрода. Недопустимы в ответственных конструкциях, т.к. существенно снижают прочность шва (ГОСТ 30242-97).
Наплывы сварных швов – излишки металла, выступающие за пределы шва. Основная причина – неправильная подача электрода (избыток присадочного материала при недостаточном прогреве основы). Частично допустимы, если не мешают сборке и эксплуатации конструкции (ГОСТ 14771-76), допустимы в некритичных соединениях (ГОСТ 23118-2012).
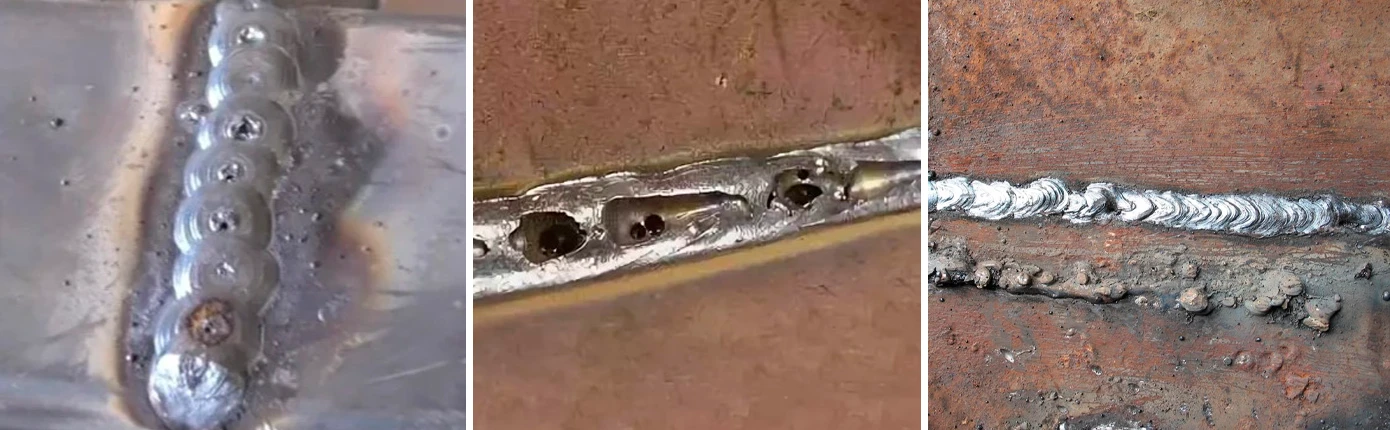
Кратеры – углубления на конце сварочного шва. Возникают из-за недостаточной заполненности при завершении шва и являются точками концентрации напряжений. Допустимы с ограничением по глубине (ГОСТ 3242-79).
Свищи – полости, соединяющие поверхность с внутренним дефектом. Возникают из-за высокой концентрации газа в сварочной зоне, слишком резком, рывковом гашении дуги. Особенно часто встречаются в углах. Недопустимы в герметичных соединениях.
Посторонние включения – примеси (шлак, флюс, металл, грязь) внутри шва. Появляются из-за недостаточной зачистки между проходами. Недопустимы в большинстве соединений (ГОСТ 30242-97).
Основные причины дефектов
Недостаточная подготовка поверхности. Загрязнения, ржавчина или масло затрудняют качественное сплавление металлов. Удаление загрязнений и окалины перед сваркой предусмотрено ГОСТ 14782-86.
- Недостаточная подготовка поверхности. Загрязнения, ржавчина или масло затрудняют качественное сплавление металлов. Удаление загрязнений и окалины перед сваркой предусмотрено ГОСТ 14782-86.
- Нарушение режимов сварки. Неправильный выбор температуры, скорости подачи электрода или защитного газа, или неподходящий электрический ток приводит к дефектам.
- Неквалифицированная работа сварщика. Ошибки оператора – частая причина дефектов, особенно при работе со сложными материалами. Сварщики обязаны соответствовать квалификационным требованиям ГОСТ 5264-80.
Методы выявления и исправления дефектов
Визуальный контроль качества сварных соединений
Это самый простой метод, требующий минимума инструментов: линейка, штангенциркуль, лупа или микроскоп. Оценка поверхности и геометрии шва, выполняется после зачистки поверхности и остывания металла. Применяется для наружных дефектов: трещин, прожогов, свищей, кратеров и т.д. Регламентируется ГОСТ 3242-79.
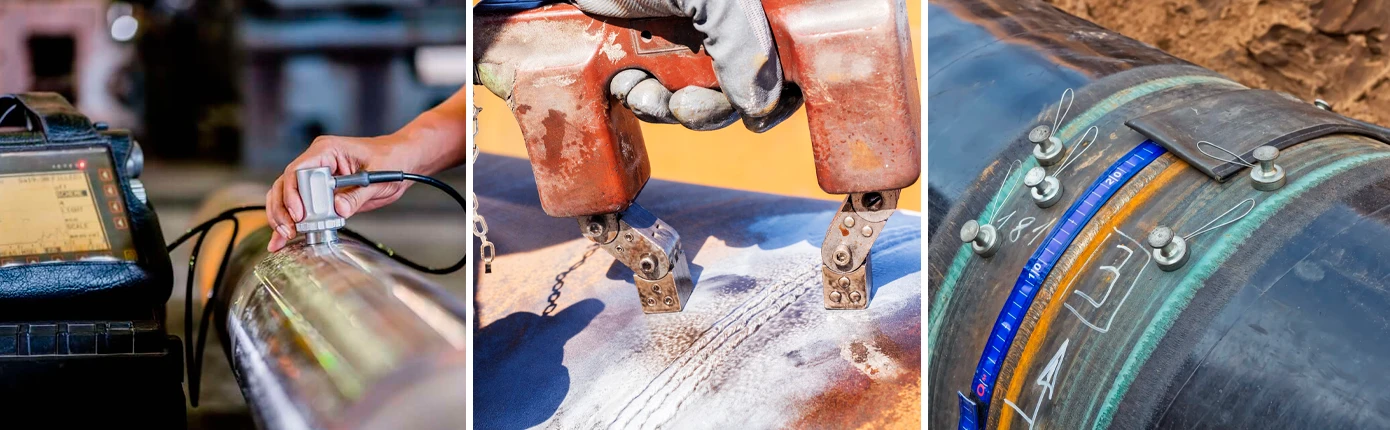
Ультразвуковой контроль сварных швов
Позволяет обнаружить внутренние дефекты, т.к. звуковые волны будут по-разному резонировать с металлом разной плотности. Методы описаны в ГОСТ 14782-86.
Радиографический контроль сварных швов
Использование рентгеновского излучения для диагностики позволяет обнаружить поры, трещины и включения. Дефекты фиксируются на пленке. Метод нормируется ГОСТ 7512-82.
Магнитопорошковый контроль
Применяется для обнаружения трещин и включений в ферромагнитных металлах, используется для очень значимых конструкций. Регламентируется ГОСТ 21105-87.
Методы ремонта и устранения дефектов
Если после сварки обнаружены дефекты, конструкция или изделие считаются бракованными до их устранения. Это особенно важно для ответственных соединений, несущих конструкций: рам, обрешеток, каркасов.
Основные действия при ремонте:
- Зачистка дефектных участков. Сварное соединение тщательно зачищают для последующей повторной сварки.
- Полная или частичная замена участка шва. При прожогах используется локальный нагрев с последующей сваркой. Участок с трещиной, кратером, свищом или непроваром вырубают, затем заваривают. Также полностью удаляют участок с наличием посторонних включений.
- Наплавка металла. Применяется для устранения прожогов, кратеров или подрезов сварочного шва.
- Шлифовка и полировка. Применяется для удаления наплывов и подрезов, коррекции поверхности. После этого важно проверить, нет ли под наплывом другого дефекта.
- Контроль после ремонта. Проведение повторного контроля согласно требованиям ГОСТ.
Качество сварных соединений напрямую влияет на эксплуатационные характеристики конструкций. Соблюдение требований стандартов, использование современных методов контроля и квалифицированный персонал обеспечивают надежность и безопасность сварочных работ. Применение ГОСТов, таких как ГОСТ 30242-97, ГОСТ 5264-80 и ГОСТ 14782-86, является залогом успешного выполнения сварочных операций.